1、Barmac9000型破碎机耐磨件的磨损机理
Barmac9000型破碎机的最大进料尺寸为57 mm,转子转速为1 000~1 800 r/min,制砂母岩是斑状花岗岩,SiO2占72. 21%,其干抗压强度为138.8~17 5.1MPa。工作时胶带机将被碎物料从设备项部给入,一部分物料通过控制器进入高速旋转的转子,转子将物料加速后以58~60 m/s的速度抛射入破碎腔中;另一部分物料瀑布式定量地溢入破碎腔,转子射出的物料与溢入破碎腔物料相互剧烈冲击,碰撞瞬间物料爆裂,经反复碰撞后,物料从57 mm破碎成4~5 mm的细散颗粒。由此可见,由这些易损件(导料板上、下耐磨板、转子抛料头、分料盘、给料孔套等)组成的转子是破碎机的心脏。而其中的给料孔套不仅要承受由上部高速射落下的高硬物料强烈冲击,而且还要将物料以较高的线速度和高的动能射向腔内。这些易损件处于磨粒磨损和冲刷磨损的复合磨损状态,工况条件相当恶劣,故要求其材质具有高硬度的同时还必须有足够的冲击韧性。
2、耐磨件材质的选用
根据主要耐磨件的磨损机理,我们选用多元高铬合金耐磨铸铁进行试制,并通过炉前孕育处理。1以提高综合力学性能。在成分控制上主要考虑要利于控制初生碳化物和共晶碳化物的数量,利于改善碳化物的形态与分布,利于坚硬碳化物能十分牢固地镶嵌在基体上。为此我们在已有研究的基础上,进行了试验。发现确定成分的关键是要严格控制碳和铬的含量及Cr/C比。适当含量的碳和铬,可获得适当量的M7C3。型碳化物;合适的Cr/C比,可基本控制奥氏体的稳定性和可硬性,从而获得理想的基体组织。本试验合金的化学成分控制见表1。
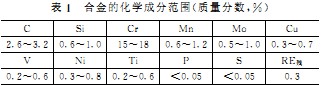
3、铸件生产工艺
试验原材料用GCr15及少锈碳素废钢、金属铬、钼铁、钒铁、钛铁,用低S、P生铁。中频感应电炉熔炼。经实验,各元素的烧损率为:C、Cr、Mo、W、Ni≤5%,V≤10%,Mn为5%~20%。为保证加入的多种合金能完全溶解,出炉温度控制在1500~1550 ℃,并用钒铁、钛铁和稀土硅铁进行炉前孕育处理,浇注温度1380~1 400℃。
采取湿型铸造,由于铸铁中合金含量高,流动性差,收缩量大,导热性差,因此在设计铸件工艺时,采取顺序凝固原则,力求消除收缩缺陷,提高致密度;同时,为了保证铸件组织致密,要加强挡渣,防止渣粒及未熔合金成为裂纹源存在于铸件中。
4、热处理工艺
在确定淬火温度前,我们对试样的硬度、冲击韧度与淬火温度的关系进行了测定(见图1、2)。可见,随着淬火温度的升高,冲击韧度缓慢降低,而硬度曲线呈现峰值,峰值附近为最佳淬火温度范围,即850~920℃:,综合考虑后,确定淬火温度为870~890℃,保温时间为2. 5~4.0 h,空冷。具体淬火温度及保温时间应根据铸件的壁厚进行适当调整,对于形状复杂的厚壁件,还必须考虑淬火加热速度,应避免因相变或高的加热温度梯度而引起高的应力,加热速度一般不高于30℃/h。一旦铸件加热至暗红色,也就是通过塑性变形温度而使应力降低得足够多时,才可加速加热。
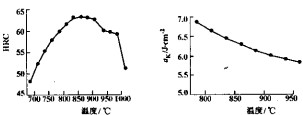
合金淬火后,必须进行低温回火处理以消除内应力,改善其韧性。回火温度控制在(200~250)℃,保温6h。
5、组织、性能及使用考核
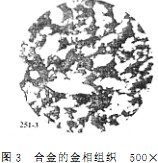
采用(德)蔡司卧式显微镜对经热处理后的多元合金铸件进行观察,其组织为马氏体基体十菊花、团块状碳化物,其中碳化物含量约占45%(见图3)。为寻找特定工况下材料韧度与硬度的最佳配合,对多元合金铸铁经热处理后的力学性能按照GB8263-87的标准进行检测,结果是:硬度64~67 HRC;冲击韧性
5. 5~6.5 J/cm2。
对Barmac9000型破碎机中的转子抛料头、分料盘、给料孔套等主要耐磨件进行装机生产考核,使用寿命为120~130 h,而进口原件约为100h,其它耐磨件的使用寿命与进口件相当。这样,使用多元高Cr合金铸铁生产的配件,破碎机的生产成本大大降低,同时也满足了工程连续高强度生产的需要,到目前,利用该材料己生产出配件10余吨,为国家节省了大量外汇。同时也为引进该机器,提高破碎效率,降低制砂成本,设备配件国产化提供了可靠的技术支持。