1、传统的自磨机
1.1传统的自磨机工作原理
见图1,矿石随简体转动,位置迅速提高,很快从受压状态转为张力状态。当矿石的重力克服离心力时,矿石就脱离简体而落下,但各种粒级矿石下落的路径是不同的,大块矿石由于重力大,上升到较低的高度时首先滑落下来,同时对相对较小的颗粒产生冲击和磨碎作用,随后往简体中心内层移动。中等块度的矿石随筒体到达较高的位置后按泻落状态滚落下来,矿石相互磨剥而形成泻落区。小块矿石随简体到达更高位置后沿抛物线轨迹落下,形成矿石瀑落区。此时的冲击力使矿石磨碎成细粒,而粒度更小的矿石则随水成为矿浆上浮到中间溢出。总之,随着筒体的转动,在不断循环过程中,矿石在冲击、磨剥和挤压的反复作用下遭到破碎和研磨,合乎产品粒度要求的颗粒随矿浆通过格筛从中部排出。
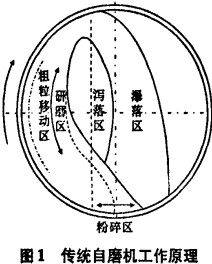
1.2传统的自磨机的缺陷
见图2,传统的自磨机的结构都是从简体的一端的中部给矿,从另一端的中部溢流排矿,底部矿石全部浸入矿浆液面下。矿石从高空落下后受矿浆浮力的影响,冲击力减弱,简体下部矿石接受的冲击力等于冲击力减去矿浆浮力,效果变差;块状和粒状矿石随简体向上旋转时,因为都处于矿浆中,泻落区研磨效果变差。
尽管传统的自磨机具有中细碎和粗磨两种功能和一次性碎磨比大的优点,但其处理能力没有充分发挥出来,使之单位功耗处理能力的优势往往不明显。
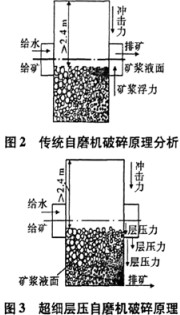
2、超细层压自磨机结构及特点
2.1超细层压自磨机的结构特点
见图3,针对传统的自磨机的结构缺陷,烟台鑫海矿山机械有限公司发明了新型超细层压自磨机,这种自磨机所处理的矿石仍从筒体的一侧简体中部
给矿,不同的是,磨好的产品是经过自磨机另一侧的下部,在离心力和矿浆压力下通过格筛强制排出。
2.2超细层压自磨机的工作原理
超细层压自磨机除具有传统的自磨机的优势和工作原理外,另外具有下列六大特点:
(1)在超细层压自磨机中,矿石从高空抛落后,没有受到矿浆浮力的影响,直接撞击筒体下部矿石,冲击力极强,将大块矿石击碎,而且在矿石内部产生更多的裂隙或致使裂隙延伸。
(2)因为矿石颗粒上本身有很多裂隙裂纹,经过上面抛落下来矿石的强烈冲击,颗粒与颗粒之间受到来自于四面八方的强大的挤压、冲击、磨剥等作用,充分发挥了层压破碎和磨剥的研磨效果,这种层压破碎和磨剥的效果显著。
(3)块状和粒状矿石随筒体向上旋转时,因为不受矿浆的影响,所以矿石表面的棱角及矿石颗粒之间进行大量的直接的反复的磨剥,也使超细层压自磨机的研磨效果远远好于传统的自磨机。
(4)由于超细层压自磨机给矿和给水是在自磨机给矿端的一侧,排矿是在自磨机的另一侧的下部.自磨机不断给进来的水会把从给矿端到排矿端磨好的合格产品加速排出,极大提高了合格产品的排矿效率。
(5)超细层压自磨机的排矿格筛是沿自磨机排矿端周边布置,在筒体连续旋转过程中,格筛始终处于排矿端下部,排矿面积火,不会产生过磨。
(6)传统的自磨机往往会出现较低的充填率,有时充填率低于20%时,就有排不出料的情况发生,所以严重影响了处理能力。超细层压自磨机由于是从下部排矿,充填率更高可达45%,而且由于磨矿浓度对磨矿效果影响不大(主要影响排矿速度),不用过多担心“胀肚”问题,提高填充率可以使矿物在相同停留磨机简体内的时间段内大大提高了冲击和研磨次数,所以处理能力更大。
(7)由于不受矿浆浮力影响,所以冲击力度强,而且冲击力不断地转化成层压力,层压力又不断地形成新的层压力,这种层压力又不断地加速,因此磨机的这种冲击能量得到了最大限度的利用;同样,因为不受矿浆的影响,所以矿石表面的棱角及矿石颗粒之间进行大量的直接的反复的磨剥,磨剥力度较强,磨机形成的这种磨剥能量也得到了最大限度的利用。所以,超细层压自磨机与传统磨机相比,磨机功耗转化成的能量得到了最大限度的利用,传统磨机很多能量被浪费掉了,由于磨矿设备几乎是选矿厂中能耗最大的设备,所以这种能耗的利用率就显得尤为重要。
3、超细层压自磨机的应用
烟台宜陶矿业有限公司(简称宜陶公司)一期工程(老系列)采用的是常规的两段破碎筛分闭路流程+一段球磨机与水力旋流器闭路流程,二期工程(新系列)采用的是一段颚式破碎机+超细层压自磨机+一段球磨机与水力旋流器闭路流程。
超细层压自磨机的在最大给矿粒度160姗的情况下,排矿粒度为:- 0.074 mm占45%;+0. 074~2 mm占45%;2.6 mm占8%;6~10 mm占2%.新系列的球磨机单台处理能力类比增加到了217.39%。
超细层压自磨机的排矿中,-0. 074 mm目占45%的产品通过水力旋流器分级后直接给入下一作业,并不通过球磨机,球磨机的给矿中,6_10姗的矿石只有不到2%的“粗粮”,其余为+0.074~0mm的矿浆,而且这其中又以大量接近合格的产品为主,所以真正实现了“多碎少磨”。采用超细层压自磨机与常规流程的设备投入和装机功率对比结果详见表1。
采用超细层压自磨机与常规流程的设备投入和
装机功率对比结果见表1。
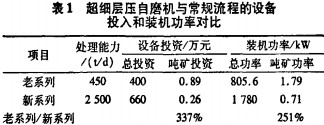
采用超细层压自磨机后,省略了中细碎筛分厂房和设备,省略了除尘机组,节省了土建投资,节省了占地面积,缩短了建设周期,降纸了生产过程中的人力成本和管理维护费用,破磨电耗下降达60%,充分体现了“多碎少磨”,是名副其实的无粉尘式的破碎磨矿节能环保型选矿工艺。
在部分矿山的矿物潮湿、黏性大,采用破碎筛分作业往往需要增加洗矿作业,而且增加相关附属设备,作业过程波动较大,如果采用超细层压自磨机与球磨机取代传统工艺,优势尤为明显。
4、结论
(L)超细层压自磨机结构新颖,碎磨效果显著。一台超细层压自磨机不仅代替了破碎筛分系统,无粉尘污染,而且在碎一磨工艺过程中,可使球磨机的处理能力增加一倍以上,相当于一台超细层压自磨机=1套中细碎筛分系统+1/2(磨矿分级系统),电力、人员及管理成本均大幅度降低。
(2)从目前看,超细层压自磨机+球磨机组合,几乎可以适应于各种类型矿石的碎磨工艺,节能效果明显。对于只需要一段粗磨的矿山,可以采用一台颚式破碎机+一套超细层压自磨机与水力旋流器闭路磨矿系统,就可以代替传统的破碎筛分系统及磨矿分级系统,投资少,流程简单,占地面积小,生产成本低,节能效果显著。
(3)对于大直径的自磨机,半自磨机、砾磨机、球磨机、棒磨机而言,传统形式的中部给矿、中部排矿的结构存在明显的缺陷,而且直径越大越明显。超细层压自磨机较传统自磨机有较大优势,有着广泛的应用前景。
(4)传统磨矿设备功耗转化成的能量浪费严重,受矿浆的浮力影响,冲击力减弱和衰减的很快;受矿浆和水的影响,磨剥力也受到了很大的影响。超细层压自磨机不存在这些影响,所以功耗及能量利用率很高。