环模的力学性能是影响环模使用寿命的重要因素,对环模进行力学分析具有重要意义。为了减少环模磨损,延长环模使用寿命,分析压块机环模工作中受力情况十分必要。目前的研究集中在对环模颗粒机的多排圆孔形环模受力分析,对环模压块机的单排方形模孔环模受力分析较少。该文在对研究颗粒机环模的基础上研究压块机环模在压块过程中的受力,明确压块机环模关键受力部位的受力情况。应用ANSYS软件研究该部位在工作过程中的应力分布及形变,为降低压块机环模磨损,优化环模结构提供一定依据。
1、压块机环模结构及工作原理
环模秸秆压块机的环模为单列方形模孔结构,模孔通常为方形,横截面的对角线一般大于25mm,长度不等。压块机环模如图l所示采用合金钢整体锻造环模坯,然后用钻头加工多个圆孔,再用铣刀铣削使圆孔成为方孔。
环模压块机主要工作部件是由固定的单列方模孔的环模和转动的偏心压轮组构成。粉碎后的秸秆物料经喂料口进入环模与压轮组间的成型腔中,随着压轮组主轴体转动将物料布满环模内表面的沟槽中,偏心压轮沿着环模沟槽内切公转和摩擦自转将物料挤压进环模孔。压轮组每完成一次公转周期就将布满环模沟槽内的物料挤压人模孔内,从而形成了燃料块的一个压层。随着物料的不断喂入和压轮组的公转、自转,便接连不断地形成无数个物料压层,相继地挤入模孔中,通过模孔中不断挤出成型。
2、环模工作受力分析
环模压块机的挤压成形过程建立在物料间存在间隙的基础上,通过压辊与环模在温度、摩擦力和挤压力等综合因素的作用下使物料间隙缩小,最终形成具有一定密度和强度的压块。根据物料在挤压过程中不同的状态,压块过程中受力情况可分为3种过程,即供料、变形压紧和挤压成形,其中在挤压成形过程时,物料所受到压辊的挤压力足以克服物料受到模孔对其的摩擦力阻力从而挤出成型。对压块过程中环模内表面和孔壁受力情况进行分析,进而研究环模模孔间主要受力的楔形部位受力。
2.1环模内表面受力分析对环模在工作过程中内侧受力情况进行研究,环模与压辊在无物料时是存在一定间隙的,环模在生产压块过程中,压辊和环模内表面间隙被物料所填充,环模内表面主要受到压辊通过物料传递的挤压力,压辊旋转通过物料传递的摩擦力。
环模压块机工作过程中,环模固定在机体上,偏心压辊通过绕主轴公转的同时自转将物料分布在环模的内侧并通过模孔挤压成型。对环模压块过程中的受力进行分析,环模在压块过程中内侧受力情况如图2所示,压辊组在主轴电机驱动下公转产生转矩r,压辊边缘在直径为D的圆周上旋转产生对物料的驱动力Q,压辊与物料和环模间相互作用产生周期性挤压力Ⅳ并通过物料传递至环模内表面,当压辊与物料接触时压辊受到物料摩擦阻力F而自转。
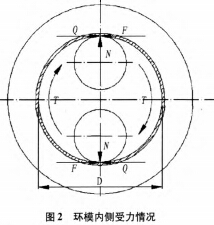
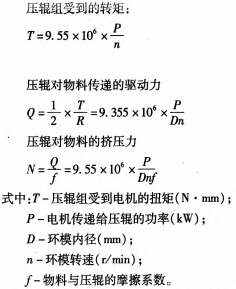
通过对在压块过程中环模内侧受力分析可知,在环模固定,压辊驱动挤压的环模压块机工作过程中环模内表面受到压辊通过物料传递的轴向挤压力与周向摩擦力的影响,通过转矩公式得出环模内表面受轴向挤压力的计算公式,环模所受到的轴向挤压力与环模的功率、环模的内径、转速及摩擦系数有关,再根据正压力与摩擦力的关系求出环模内表面所受摩擦力。
2.2环模孔内受力分析环模压块机在压辊的作用下将物料通过模孔挤出成型。在挤压过程中,物料在模孔内受到压辊传递的轴向挤压力,同时物料受到环模孔壁对其的摩擦阻力。模孔中的物料挤出需要满足的条件是物料所受的轴向挤压力大于物料与环模孔壁间摩擦力。为研究压块过程中方形模孔内表面的受力情况,压块过程中孔内的物料压块视为整体,受力分析如图3所示。
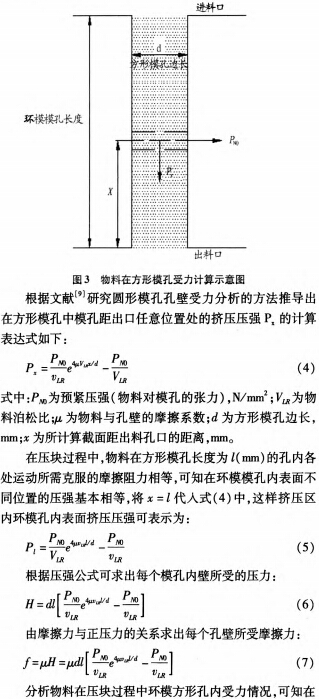
分析物料在压块过程中环模方形孔内受力情况,可知在压块过程中模孔内壁主要受到物料对其的挤压力和摩擦力,挤压力与模孔的结构特性和物料的属性有关。
2.3关键部位受力分析经过对压块机环模内侧及模孔在工作过程中所受物料的作用力研究,可知在进行压块时环模受到压辊通过物料传递作用于内表面的轴向挤压力和周向摩擦力,环模的模孔内壁受到物料对其的挤压力以及摩擦力的影响,而这些力主要作用于模孑L间的楔形部位,楔形部位为压块过程中的关键受力部位,该部位当压辊运动到上方时受力达到最大,其受力情况如图4所示,楔形部位受到压辊通过物料传递的周期性轴向挤压力N和摩擦力F,物料在模孔中对其侧壁的挤压力H和摩擦力f。
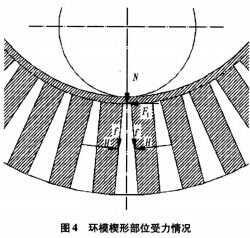
3、仿真
压块机的环模在压辊对物料周期性压缩的作用下产生接触挤压应力,环模在此应力循环作用下楔形部位所受局部载荷很大。经过对环模的受力分析可知环模的楔形部位所受载荷的情况,为验证该部在压块过程中是否满足设计要求,并研究该部位在在受力后的磨损情况,应用ANSYS软件对楔形部位进行静力分析,研究楔形部位在压块过程中受力后的应力分布和发生的形变。
以生物质秸秆压块成套设备数据模拟进行仿真分析,成型机电机转动功率P= 45 kW,成型机额定转速n=166r/min,成型机模孔数量为36个,模孔规格为32 mm x32 mm方形模孔,成型模孔深Z= 130 mm,成型环模内径为D=493mm,压轮个数为2,压轮与环模间间隙1mm,物料与压辊的摩擦系数为,=0.6。物料的泊松比=0.3,物料与环模的摩擦系数为p=0.38,物料预紧压强(物料对模孔的张力)根据武凯等人所做试验得出结果为PNO=4.8 KPa。环模的材料选用45号钢,弹性模量为210CPa,泊松比为0.3。
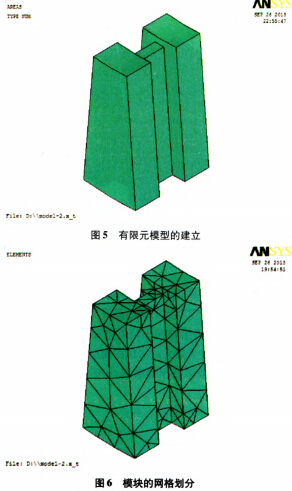
3.1模型建立及网格划分为分析压块机环模楔形部位在工作过程中所受应力及形变,将环模整体拆分为如图5所示的局部模块进行ANSYS分析。
在ANSYS13.0中对原有的单元类型进行了整合,该模块选取设置网格类型为SOLID185单元进行划分,划分后如图6所示,并定义模块的材料属性,弹性模量为210 GPa,泊松比为0.3。
3.2加载载荷及求解根据环模工作原理,模块在仿真过程中约束添加在模块外侧表面,结合压块机工作过程中受力情况,模块受到压辊通过物料传递的轴向挤压载荷和周向的摩擦载荷,载荷添加在模块楔形部位的上表面,同时也受到模孔内物料对模块侧壁的挤压载荷和摩擦载荷,载荷施加在楔形部位的两个侧面,载荷数据根据前文参数计算得出。
通过应力云图分析其结果表明,环模的楔形部位所受最大应力为155 MPa,由于45号钢力学性能为抗拉强度不小于600 MPa,屈服强度不小于355 MPa,楔形部位满足使用要求。再根据如图8所示形变图观察其形变位移。
由模块楔形部位形变图可知楔形部位在压块过程中受力最大形变位移量为0.015 6mm,形变量较小,不影响物料通过环模挤压成型。
3.3结果与分析通过对模块的楔形部位进行ANSYS分析,可知在压块过程中环模的楔形部位受力后的轴向应力分布。应力沿轴向不均匀分布且越与压辊接近所受到的应力越大,应力最大点出现在楔形部位两端与环模整体相接处,将会造成该处出现磨损,在压辊周期性载荷作用下易引起疲劳断裂。
楔形部位在压块过程中受力后发生了变形,形变位移沿切向呈不均匀变化,中间位移量较大两端较小,位移方向与压辊运行方向相关,最大位移出现在楔形部位顶端,将造成该部位磨损较大。
4、结论
通过研究环模压块机环模在工作过程环模内侧以及模孔中受力情况,分析模孔间的楔形部位为关键受力部位,应用ANSYS软件分析环模楔形部位受力后应力分布及形变,得出以下结论:
(1)通过对环模在工作过程中环模内侧与压辊受力情况及物料在模孔中与孔壁受力情况的研究,分析压块机环模的关键受力部位,得出环模模孔间的楔形部位为主要受力部位。
(2)应用ANSYS软件分析环模压块机在工作过程中关键受力的楔形部位应力分布及形变,楔形部位轴向内侧所受应力较大,该部位顶端单侧发生变形因而较易磨损,在周期载荷作用下疲劳断裂也是环模楔形部位的一种失效形式。
(3)根据对仿真后得出的环模受力情况进行研究,环模的楔形部位失效主要为单侧磨损,物料均匀分布有利于改善受力。
(转载请注明:30码期期必中秸秆压块机)